Capabilities
Surface Finishing
GSM Aluminium can offer a range of different finishes / colours to meet our customers’ requirements, whether to enhance the appearance or offer durability and protection.
A 5 Star Rated Service For All Customers
Fast Delivery Of Fully Fabricated & Finished Parts
A Focus On Quality Extrusions And Attention To Detail
Working With UK Providers, Minimising Our Carbon Footprint
Anodising
The anodising process produces a natural oxide coating on the surface of the aluminium making it stronger and more resistant to wear. The coating is produced by sending an electric current through a diluted acidic solution Depending on the solution used and the processing conditions, we can create a variety of colours, thicknesses, densities and hardness, to suit various briefs.
Once the aluminium has been anodised, the product will be more hardwearing due to its thicker, corrosion resistance layer.
We operate two anodising plants comprising of 38 tanks, including brightening, anodising, AC colouring and Nickel colouring as standards. Each plant produces silver, bronze, black and nickel from 3000mm to 8500mm, in thicknesses of 5 to 25 microns.
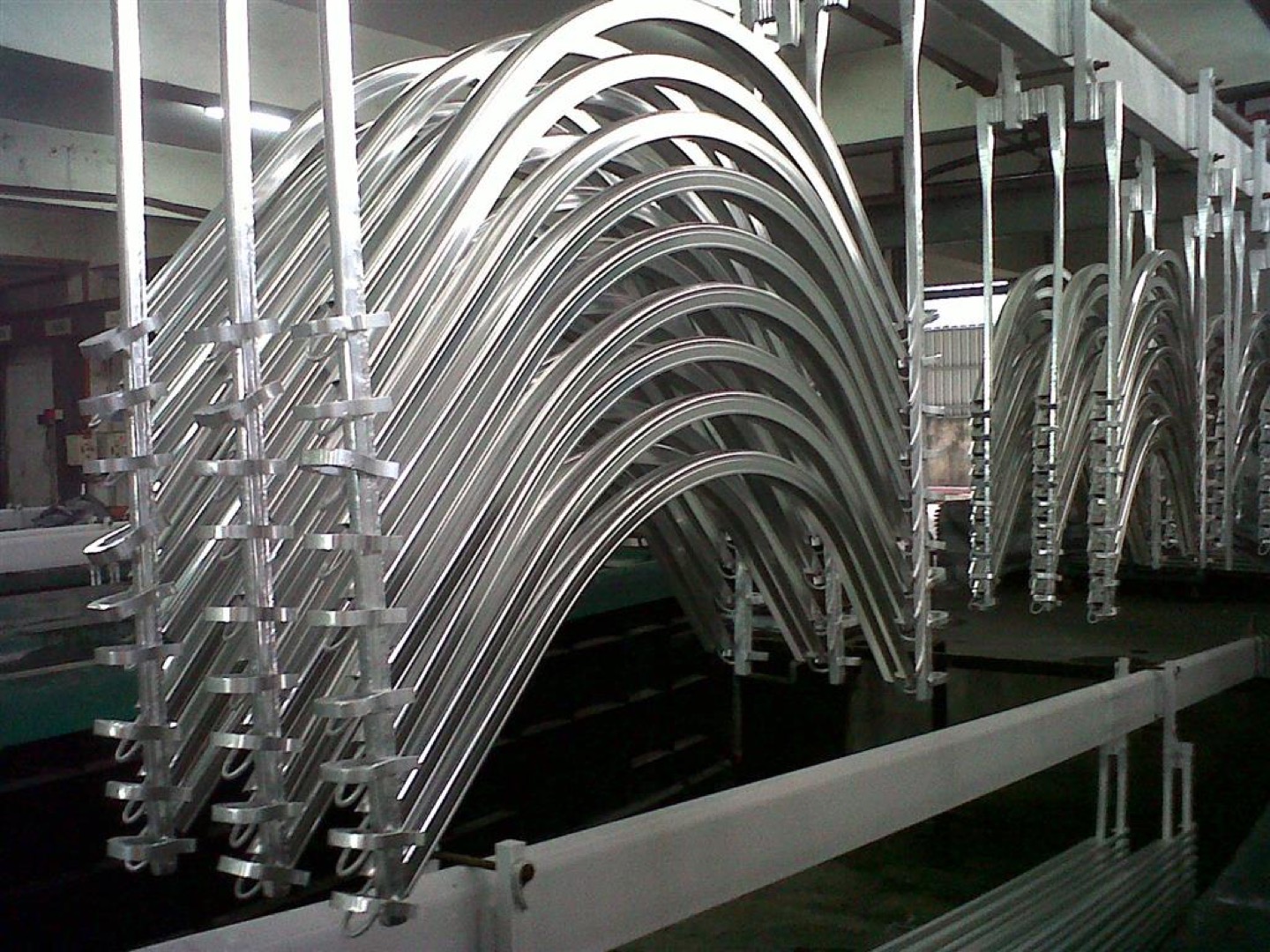
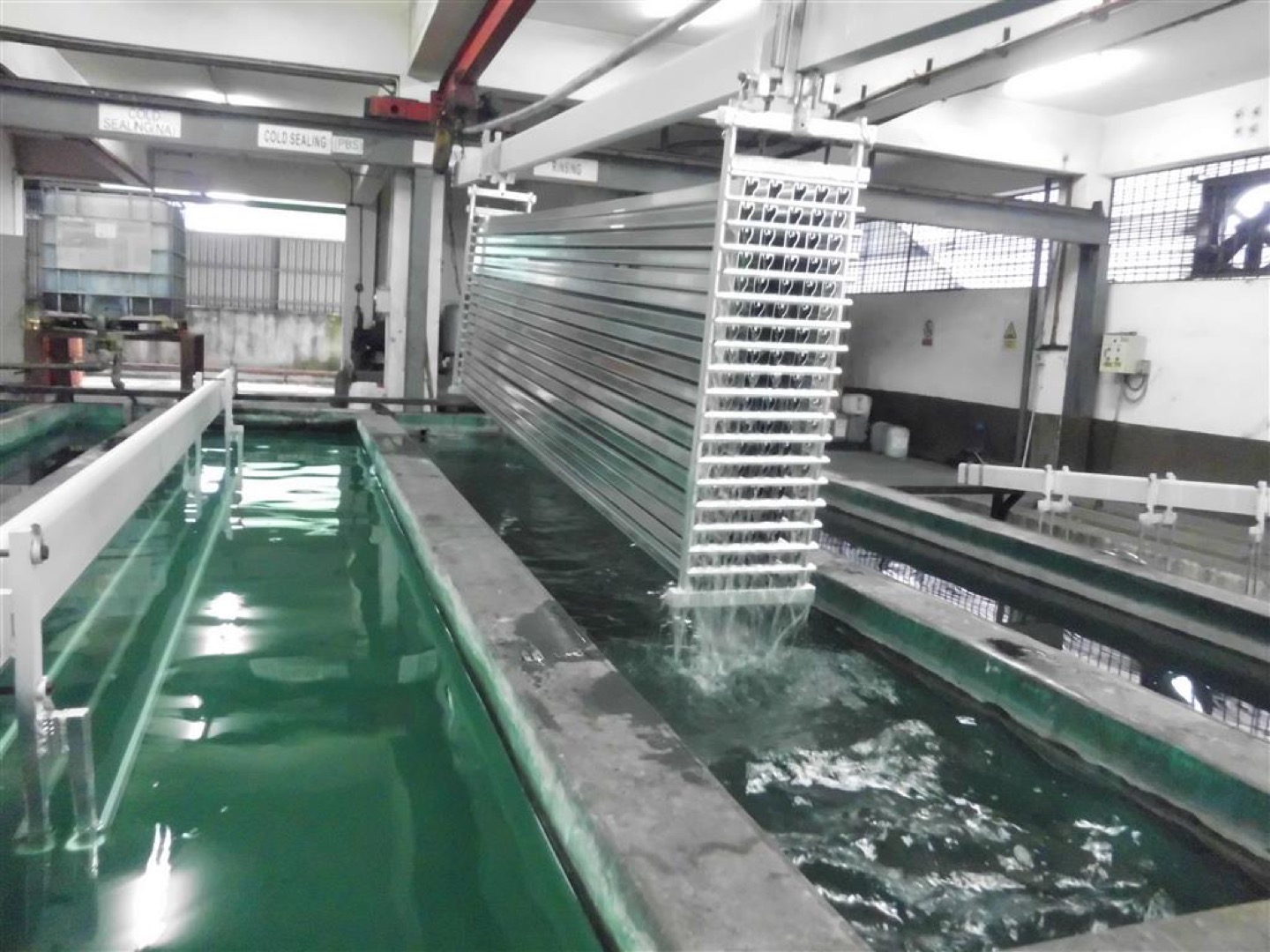
We operate two anodising plants comprising of 38 tanks, including brightening, anodising, AC colouring and Nickel colouring as standards. Each plant produces silver, bronze, black, nickel from 3000mm to 8500mm, in thicknesses of 5 to 25 microns.
During the anodising process, a strong contact is made between the aluminium profile and its carrier frame resulting in visible clamp marks measuring 25mm at both ends of each profile. These can be cut off if required, to produce a net usable length.
We offer a sandblasting pre-treatment to minimise the etching time during the anodising process. This process gives a consistent soft sheen surface finish once the profiles are anodised. Extrusion and weld lines become much less noticeable.
Hard Anodising
This is a type of sulphuric acid anodising, where process conditions have been pushed in a certain direction to achieve significantly harder, thicker, denser films. Applications provide greater resistance to wear, corrosion, temperature effects etc.
It is commonly used for components in the military, aviation and automotive industries, and for pneumatic cylinder tubes, valve spools and hydraulic parts. Hard anodising gives increased service life and provides greater corrosion resistance.
Typical anodising thickness ranges from 25- 50 microns.
It is typically used on component extrusions, up to 1200mm in length.
Polyester Powder Coating
Available in Standard RAL colours in matt, semi-gloss or full-gloss levels, produced under the Qualicoat certification.
Large production capacity.
Metallic / Special RAL colours also available. Colour matching to customer requirements.
Maximum length of powder coated profiles on the horizontal paint line is 6.5 metres. Maximum length of powder coated profiles on the vertical paint line is 7.5 metres.
Short length painting possible dependant on specific project.
Mechanical Polishing
Polishing is a critical stage of our process before anodising, to achieve a highly reflective, blemish free finish.
Using automatic flatbed polishing machines we can polish up to 6.5 metres, producing a consistent gloss level on the surface.
This process is used for shower cubicles, the automotive industry and furniture profiles.


Mechanical Brushing
Using automatic flatbed machines, we can polish up to 6.5 metres. These machines are set to carefully control the applied pressure of brushing and the brushes can be set for each individual profile shape to achieve a perfectly consistent finish. This finishing option is becoming more and more popular and can be added to all our anodising colours to give a huge selection of added value choices within a product range.
Brushing can be done linearly along the profile, or spiral brushed (around the circumference of tubes)
Chemically Bright Polished
One of our key areas of expertise is to produce a mirror-like surface finish quality, thanks to our two Electro-Chemical Brightening lines, fully integrated within our anodising plants.
We can chemically bright anodise profiles from a small component size up to a 6.5 metre bar length.
To pass our internal quality inspection criteria, the profiles must be free of defects not visible at a distance of 1 metre and must appear visually uniform, free of streaks and stains on the primary profile surface area.
The Electro-brightening process provides a much brighter finish compared to a natural anodised profile. The surface gloss level is even higher when the profile is mechanically polished beforehand.
The profile surface gloss level (when measured with a glossmeter at 60°) is as follows:
Finish | Surface gloss (gloss) |
Profiles with chemical bright anodising | 330 GU ≤ gloss ≤ 450 GU |
Profiles with mechanical polishing and chemical bright anodising | 550 GU ≤ gloss |
Finish | Average thickness of oxide layer(Th.) |
Profiles with chemical bright anodising | 5 μm ≤ thickness ≤ 8 μm |
Profiles with mechanical polishing and chemical bright anodising | 2 μm ≤ thickness ≤ 4 μm |
AC Colouring
Profiles can be enhanced with a range of different anodised colours. Using standard techniques and varying the voltage and time in the acidic bath can achieve a range from silver – bronze – black and Nickel.
The addition of dyes allows a vast array of colours. Typically available on shorter length, component parts. Contact us for more details on a specific requirement. Colours include Nickel variants and rainbow colours.

HOW IT WORKS
Our Process
We quote for aluminium and tooling based on your technical drawings
You accept our quotation and terms of business
We complete technical drawings and issue for your approval
You place the bulk order
Bulk or call-off delivery to you
Dispatch of goods to GSM warehouse
Sample sent for you approval, release of bulk production
Extrusion and fabrication tooling manufactured
OUR GUARANTEE
Quality & Standards
Extrusion and tolerances are according to EN755-9 and EN12020-2.
Our own extrusion factories, as well as our other suppliers or sub-contractors, are chosen based on their capacities to integrate all their manufacturing and surface finish processes under one roof, allowing for greater cost competitiveness and stronger quality control.
All our efforts are focused on ensuring that our customers receive the best quality possible. GSM Aluminium is ISO 9001 accredited. We continuously monitor our internal quality control systems, manufacturing processes and very importantly that our customers are fully satisfied. Historically, GSM Aluminium can demonstrate that overall, only 0.13% of our delivered profiles were rejected by customers.
Our own factories and our suppliers are all ISO 9001 and 14001 registered.
EXPERT & COMPETITIVE
Why Choose Us?
30+ Years Experience
GSM Aluminium has shown steady and sustained growth as a supplier and distributor of bespoke aluminium products to both the UK and Europe.
Highly Trained & Qualified
Resulting in an efficient and professional customer service, from technical sales to accounts and logistics.
Stock Holding
GSM has the ability to manage stock for customers, leading to timely order placements, ensuring continuity of supply and keeping lead-times to a minimum.
ISO Accreditation
Ensures continued monitoring of systems, supplies and customer satisfaction. In the year GSM can demonstrate only 0.13% of rejected profiles.
TESTIMONIALS
Client Feedback
CONTACT US
Aluminium Extrusions Are Our Passion
If you're looking for a competitive UK aluminium extrusion profile manufacturer and stock holder with the capacity to deliver on time contact us today.